Selena Group, a global manufacturer and distributor of construction chemicals, and Covestro, a world-leading supplier of high-tech polymer materials, have engaged in cooperation leading to the development of a reduced carbon footprint formulation for Selena’s best-selling Tytan Professional® Ultra Fast 70 foam. The product uses innovative, low-carbon MDI (methylene diphenyl diisocyanate), an organic chemical compound containing bio-based feedstock accounted for using the mass balance approach. This helped reduce the foam’s carbon footprint by about 45%* compared to the previous version of the product that used fossil-derived feedstock. This innovation maintains the product’s excellent thermal insulation properties and additionally contributes to reducing the building’s embedded carbon footprint.
By uniting their forces, Selena Group and Covestro forged a strategic alliance geared towards co-creation and driving sustainable change in the construction industry. The efforts undertaken by the R&D teams have resulted in the development of a range of single-component polyurethane foams with a reduced carbon footprint that improve the energy efficiency of buildings. The Tytan Professional® Ultra Fast 70 foam – recognized by builders, characterized by a remarkable yield of up to 77 liters per can and a very short cut time of merely 20 minutes – now incorporates 30% of bio-attributed MDI calculated using the mass balance approach, as validated by the ISCC Plus standard, which certifies the use of bio-based raw materials and their precise allocation in the production process. The foam has been successfully used for the installation of windows and doors, especially in projects requiring quick assembly and high efficiency of construction works. Now, following the changes, it has become even more environmentally friendly while significantly reducing the carbon footprint embedded in buildings.
“Today, sustainable business no longer necessitates compromises between efficiency and quality. This claim is perfectly evidenced by our latest solution: with identical molecular composition, the bio-based content does not affect the quality or properties of the final product, while complying with stringent environmental standards and responding to future trends. This is a real proof of the success of the collaboration between two international manufacturers who are striving for innovation,” said Mirosław Truchan, Head of Marketing Division Windows & Doors of Selena Group.
Selena R&D team has a long track-record of achievements, with a focus on sustainability as a response to the challenges related to the decarbonization of construction by 2050. The Group also created its proprietary feedstock – BIOSELENOLS® – polyester polyol, 100% bio-based, used in Selena’s another product: Tytan Professional® Low-Ex Green foam. The efforts of the two companies are in line with the principles of the European Green Deal, Fit for 55 and the overarching goal of achieving carbon neutrality in the building sector by 2050. From the local point of view, these actions embody Selena Group’s sustainable development pillars referred to as IFEEC (Investors, Finance, End Users, Employees, Climate), notably in the areas of End Users and Climate.
*reduced carbon footprint of the Ultra Fast 70 foam with bio-attributed, mass-balanced MDI compared to the same product with standard fossil-derived MDI; carbon footprint calculated for the cradle-to-gate life cycle
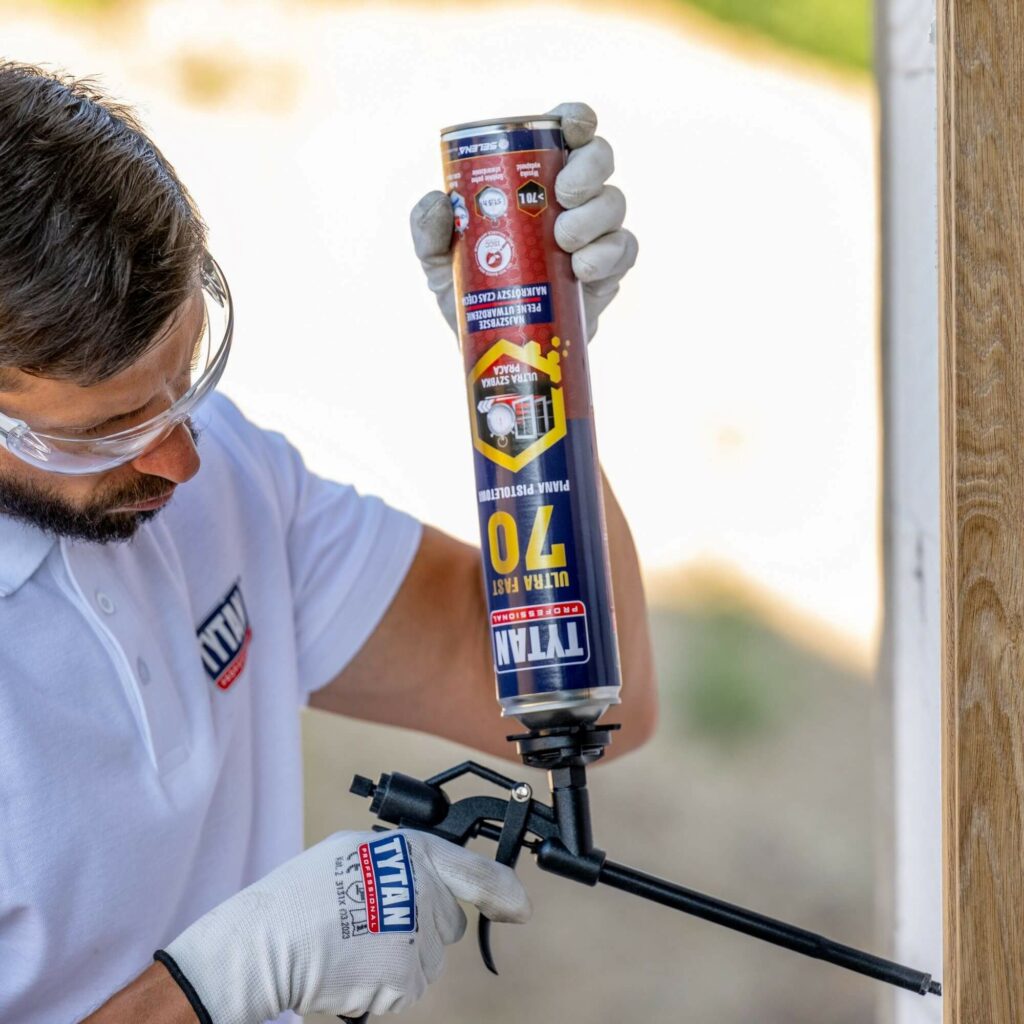
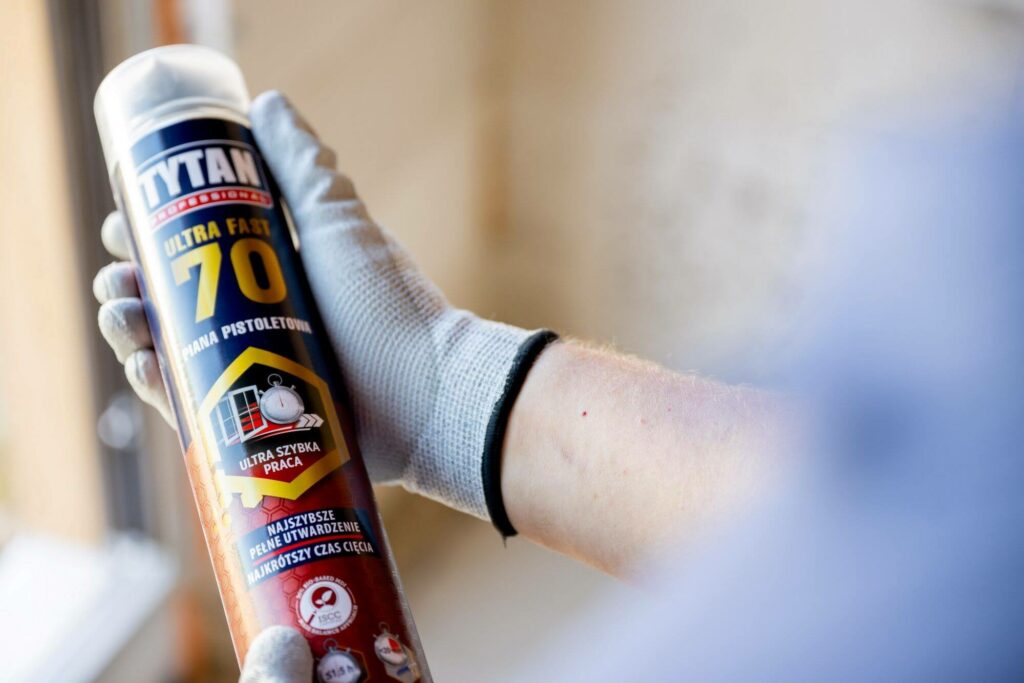